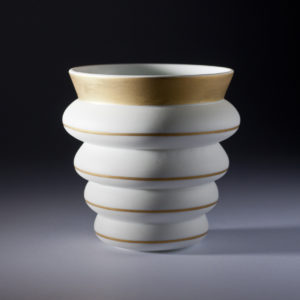
Naissance de l’attrait pour la matière porcelaine
Depuis le début de l’ère chrétienne jusqu’au XVIIe siècle, des objets chinois exotiques, recherchés, rares et chers, sont acheminés en Europe par voie terrestre (route de la soie) ou par voie maritime ouverte par Marco Polo.
Alors que la fascination pour la porcelaine se développe dans toute l’Europe, un Jésuite, le Père François-Xavier d’Entrecolles, né à Limoges le 25 février 1665 et mort à Pékin le 2 juillet 1742, rapporte par un récit détaillé la fabrication de la porcelaine en Chine, en 1712 et en 1722. Ce récit décrit de nombreuses étapes de fabrication de la pâte, des formes, du décor, des fours… mais il ne permet pas de percer complètement le secret de la porcelaine.
Dans toute l’Europe se développe la volonté de produire une porcelaine qui «pourra rivaliser avec celle des Indes orientales»
C’est à Meissen, en Saxe (actuelle Allemagne) que Johann Friedrich Böttger, un alchimiste, perce le secret de la porcelaine en 1710.
En 1751, la manufacture Paul Hantons fabrique une porcelaine dure à Strasbourg.
La recherche du minerai et la mise au point de la pâte
Nous savons aujourd’hui que les gisements de kaolin se forment au dépens de la décomposition des roches primaires granitiques (roches acides), que l’on trouve dans plusieurs régions de France : Limousin, Auvergne, Bretagne, Drôme…
Découvert dès 1768 sur les communes de Saint-Yrieix-la-Perche, puis celles de Marcognac, Saint-Paul-la-Roche, La Jonchère-Saint-Maurice… la présence du kaolin ouvre enfin la possibilité au royaume de France de fabriquer sa propre porcelaine.
Des essais sont menés à Sèvres et à Limoges. Sèvres produit une porcelaine dure en 1765, et Limoges parvient à produire une porcelaine dure en 1771.
La toute première manufacture de porcelaine de Limoges est en fait une «Fayancerie Royalle» fondée à Limoges en 1736 par Massié. C’est dans cet établissement travaillant la faïence grâce à un agrément royal que l’on commença les essais de fabrication et de cuisson de la porcelaine de Limoges à partir de 1770.
Le développement des fabriques de porcelaine se fit à partir de 1773 :
Fabrique du Comte d’Artois (1773), La Seynie (1774), Manufacture Royale (1784), Monnerie (1795), Alluaud (1797), Tharaud (1817), La Fabrique de Saint-Brice (1825), Coussac-Bonneval (1825), Pouyat (1832), etc.
Les fabriques naissent et meurent, s’achètent, se vendent, se modernisent, déménagent… mais certaines d’entre elles sont toujours en activité aujourd’hui.
Les premières manufactures et leur fort développement au cours du XIXe siècle
L’essor des manufactures s’est fait en vendant de la porcelaine dans toute la France, en particulier des services de table complets pour des mariages ; et aussi par l’export à l’étranger, en particulier vers les Etats-Unis.
Année | 1837 | 1875 | 1913 |
---|---|---|---|
Fabriques | 24 | 20 | 30 |
Fours | 40 | 85 | 114 |
Ouvriers | 4550 | 8450 | 8200 |
Chiffre d’affaire en Francs | x | 4 750 000 | 11 800 000 |
L’exemple de la manufacture Haviland
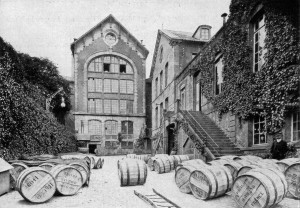
Année | Nombre de colis livrés |
---|---|
1842 | 753 |
1843 | 909 |
1844 | 1847 |
1845 | 1630 |
1846 | 2087 |
1847 | 2650 |
D’abord acheteur de blanc, Charles Haviland assurait le décor avant d’expédier le plus gros de sa production aux USA, pour lesquels ses décors étaient conçus et où il bénéficiait d’un excellent réseau de distribution. Pour faire face à son formidable succès, il forma de nombreux décorateurs et se mit à produire lui-même sa porcelaine blanche.
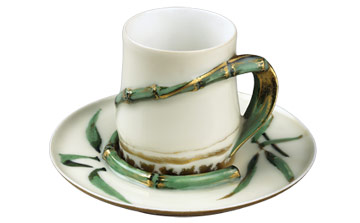
Au XIXe siècle se construit un tissu industriel propice à l’activité des manufactures
Plusieurs carrières de kaolin sont ouvertes en Haute-Vienne, ainsi que des séchoirs à kaolin et des moulins assurant le traitement des matières premières et la préparation des pâtes.
Il y avait 16 moulins en activité en 1837.
«L’Usine du château» à Aixe-sur-Vienne, très ancien moulin à pâte, est toujours en activité sous le nom KPCL (Kaolin et Pâtes Céramiques du Limousin), groupe Imerys.
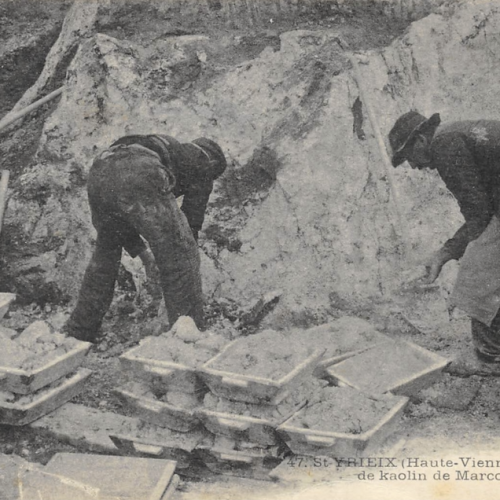
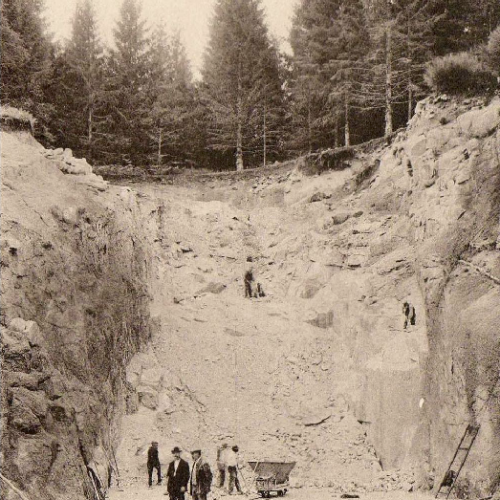
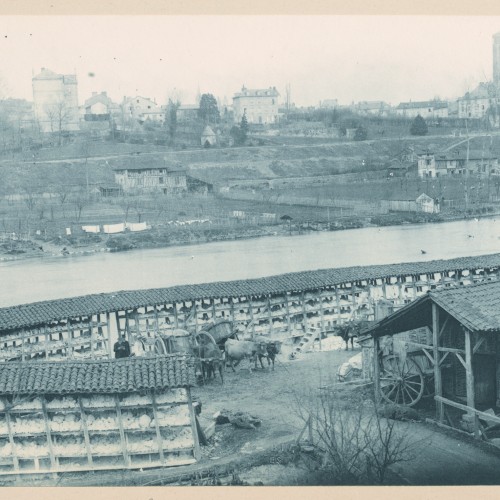
Le bois nécessaire aux cuissons
Le bois était coupé par des bucherons en Creuse (département voisin) ou dans l’Est de la Haute-Vienne, à plusieurs dizaines de kilomètres, avant de transiter sur plusieurs cours d’eau affluents de la Vienne pour rejoindre Limoges où le bois était arrêté par un ramier. Les bucherons et les flotteurs de bois ont constitué une corporation puissante car leur activité était déterminante pour l’industrie de la porcelaine.
Année | Volume de bois flotté sur la Vienne |
---|---|
1789 | 10 000 stères |
1814 | 23 000 stères |
1855 | 107 000 stères |
1865 | 45 000 stères |
En 1881, le flottage du bois s’arrêta au profit du transport ferroviaire.En 1897, le ramier de Limoges fut démoli.
L’activité industrielle aux XIXe et XXe siècles
L’industrie de la porcelaine a connu des ralentissements dans son développement durant la guerre de 1870, puis lors des deux Guerres Mondiales.
La production a baissé en 1914-1918 pour des raisons d’effort de guerre et par manque de main d’oeuvre, les hommes étant partis au front.
En 1939-1945, la production a encore plus fortement baissé pour des raisons de restrictions liées à l’effort de guerre puis à l’occupation : plus assez de matières premières, restrictions sur le charbon et sur le bois…
Mais après chaque période difficile, les industriels de Limoges ont rapidement renoué avec la croissance et les bénéfices.
L’activité industrielle après 1950
Des années 1950 à nos jours, les manufactures font appel aux designers : Raymond Loewy, Roger Tallon, Marc Held, Martin Szekely, Olivier Gagnère, Hervé Van Der Straeten, Andrée Putman, Jean-Charles de Castelbajac, Sylvain Dubuisson, Andrea Branzi, etc.
À partir des années 1980, les habitudes de consommation ont changé et l’industrie a connu un net recul de ses ventes. De nombreuses entreprises ont du être restructurées ou ont disparu.
Aujourd’hui, les industriels sont condamnés à se réinventer en diversifiant leurs activités sur le luxe, le bijou, les objets décoratifs, les partenariats avec des designers, tout en continuant la production des services de table traditionnels.
Les principaux acteurs du marché aujourd’hui
- Environ 20 entreprises à l’heure actuelle
- 1100 emplois directs dans les entreprises de porcelaine de Limoges
- 300 emplois induits
- Environ 120 Millions d’Euros de Chiffre d’Affaire annuel
- 70% de la production part à l’exportation, dont la majorité aux USA
- Les manufactures les plus illustres sont : Bernardaud, Haviland, Raynaud, Royal Limoges, R. Haviland & C. Parlon, J. Seignolles, Arquié, Carpenet, Pergay, Médard de Noblat, Jean-Louis Coquet, Sylvie Coquet…
L’action d’Esprit Porcelaine depuis 30 ans, regroupant des artistes confirmés et une jeune génération.
Esprit Porcelaine Créateurs à Limoges est un collectif de designers céramistes qui imagine les objets d’aujourd’hui et de demain. Par le brassage de différents horizons artistiques: designers, artisans d’art, concepteurs de formes, artistes… l’association présente une dynamique de création en perpétuel renouvellement.
Vivier d’artistes, laboratoire d’idées, les créateurs d’Esprit Porcelaine –à travers des particularités personnelles qui vont toujours dans le sens de l’innovation –oeuvrent dans un souci constant de renouvellement de l’image qu’ils veulent développer de la porcelaine de Limoges.
Ancré dans son territoire, Esprit Porcelaine coopère étroitement avec des entreprises locales pour la fabrication et l’édition de ses modèles.

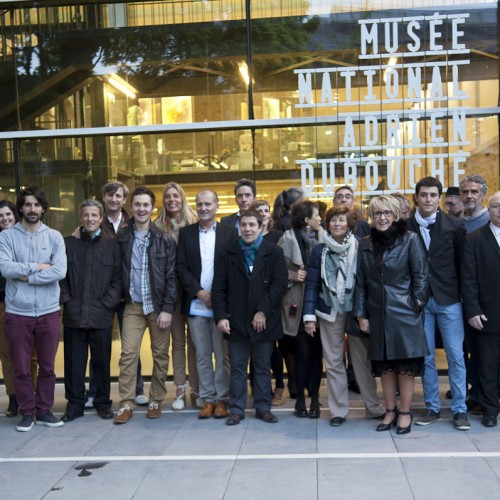
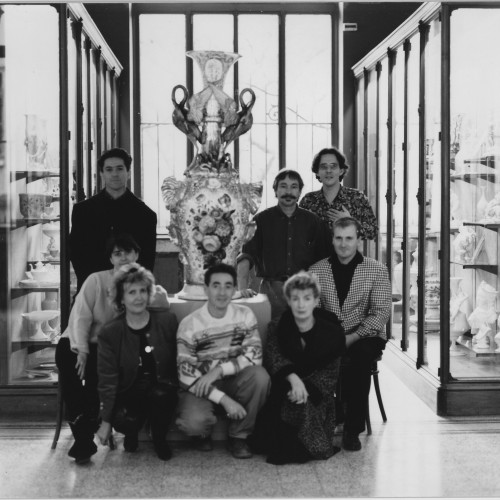
La formation des céramistes et porcelainiers de demain à Limoges
Lycée des arts et métiers «Le Mas Jambost»
– Brevet de Métier d’Art céramique artisanale
– Certificat d’Aptitude Professionnelle de décor sur céramique
Association de la Formation Professionnelle de l’Industrie
– Brevet de Technicien Supérieur en céramique industrielle
Ecole Nationale Supérieure d’Art
– Diplômes nationaux supérieurs d’art et de design
– Post-diplôme en céramique contemporaine
Ecole Nationale Supérieure de Céramique Industrielle
– Ingénieurs en céramique industrielle
Un IGP (Indication Géographique Protégée) pour la porcelaine de Limoges
Un projet d’IGP (Indication Géographique Protégée) vise à labeliser et contrôler la provenance des produits estampillés «Porcelaine de Limoges -France» afin d’éviter les contrefaçons et la fraude, et préserver le tissu industriel local. Ce label exige que le produit soit entièrement manufacturé dans le département de la Haute-Vienne : fabrication de la forme et du décor.
La fabrication – Le plâtre
Le plâtre constitue le matériau principal pour la création de formes. Il est utilisé aussi bien pour les modèles que pour les moules, les possibilités de dosage du plâtre lui conférant une grande polyvalence.
Pour la réalisation de modèles, on peut tailler, graver et sculpter le plâtre, mais aussi le traîner et le tourner à l’aide de calibres, de gabarits et de tournasins.
Le plâtre, par sa porosité, est idéalement adapté à la réalisation de moules pour la porcelaine : le moule en plâtre donne la forme en même temps qu’il absorbe l’humidité ; il peut servir à prendre des empreintes sur des modèles sculptés, ou d’après «nature».
En principe, et en raison du caractère déterminant de ces ateliers, chaque manufacture possède son atelier de moulage où l’on travaille le plâtre. C’est un atelier séparé des autres afin d’éviter que le plâtre ne contamine la pâte de porcelaine. C’est aussi l’atelier dans lequel s’exprime le caractère créatif de chaque manufacture.
Dans cet atelier travaillent des modeleurs, qui créent les formes : modèles et moules échantillon.
Puisque les moules ne peuvent servir que 30 à 50 fois, il faut les renouveler régulièrement. C’est pour cette raison que l’on fabrique des matrices permettant de dupliquer et de renouveler les moules.
Après le modeleur intervient l’établisseur. Il fait le premier moule et les matrices à partir des modèles ou des moules échantillons. Les matrices sont réalisées en plâtre, en résine ou en silicone.
Ensuite, le couleur de moule fabrique les moules en série à partir des matrices.
Le travail des modeleurs et des établisseurs est essentiel dans toute fabrique, et comme ce savoir-faire est spécifique, il ne peut-être réalisé que par des employés spécialisés.
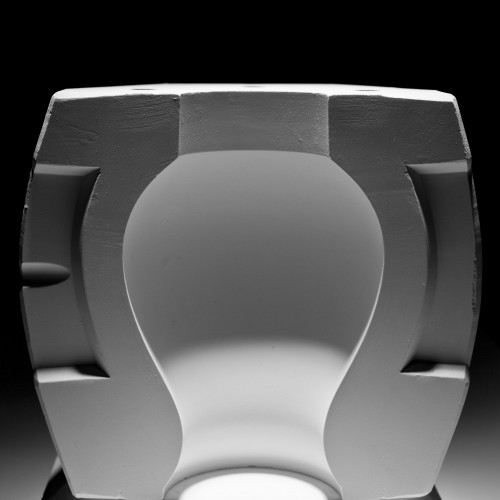
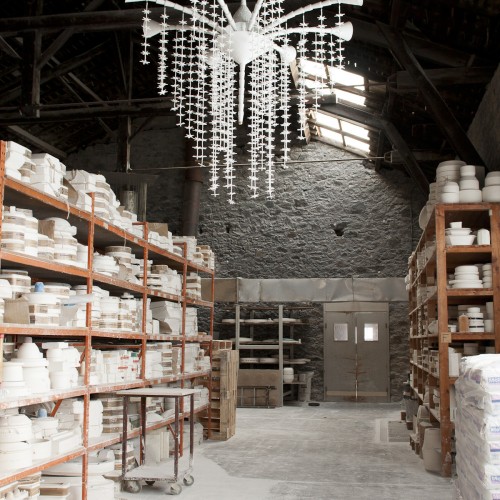
La fabrication – La pâte
La porcelaine n’est pas une «terre» existant à l’état naturel, mais une «pâte» conçue par l’homme à partir de trois roches principales :
le kaolin, le quartz et la pegmatite orthose.
La composition globale est de :
50% de kaolin
25 % de feldspath
25% de quartz
Dans les barbotines, on ajoute une petite quantité de défloculant (carbonate de sodium, silicate de sodium) qui permet à la pâte d’être fluide avec le minimum d’eau, et qui lui évite de figer.
Le kaolin est une argile primaire très réfractaire. Il se transforme en cristaux de mullite baignant dans une masse vitreuse de quartz fondu lors de la cuisson à haute température.
Il entre pour 50% dans la composition de la pâte
La pegmatite orthose est une roche potassique ayant pour effet d’abaisser le point de vitrification de la pâte.
Elle contient du feldspath et du quartz et entre pour 40% dans la composition de la pâte.
Le Quartz entre pour 10% dans la composition de la pâte.
Très réfractaire, il devient vitreux vers 1380°C, grâce au feldspath qui sert de fondant.
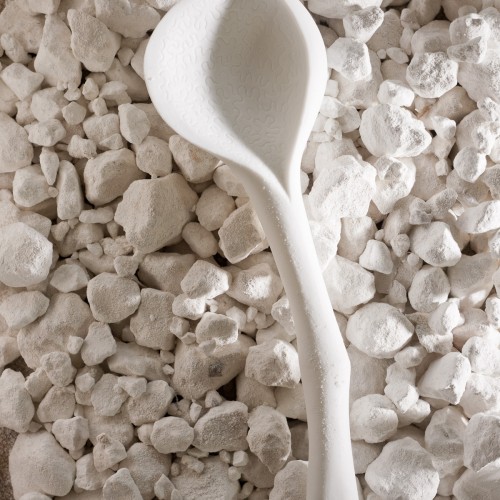
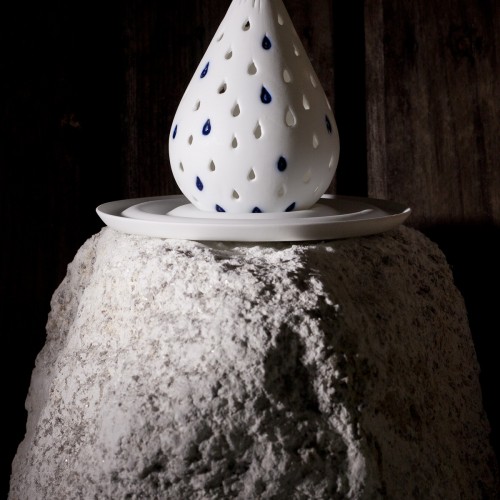
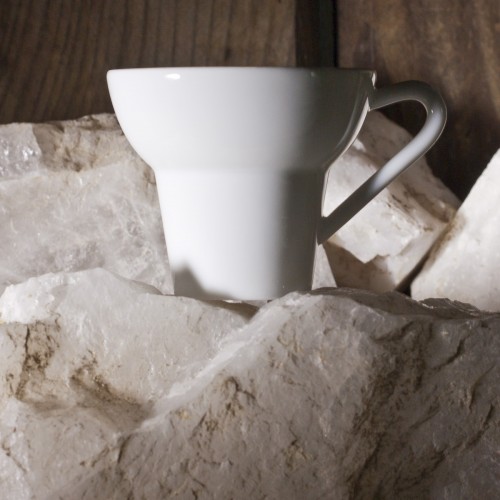
Les différentes formes de la pâte
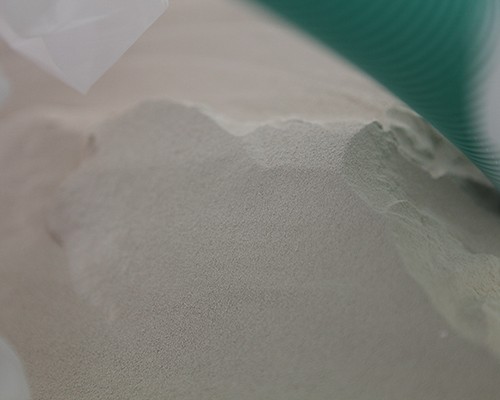
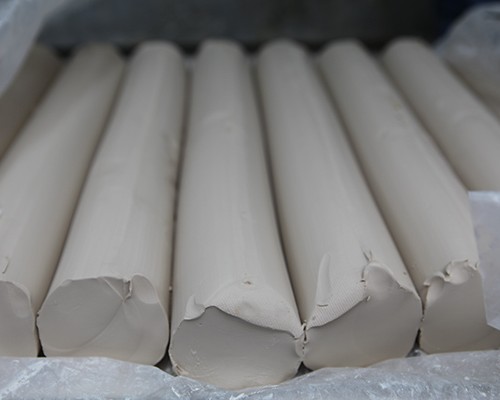
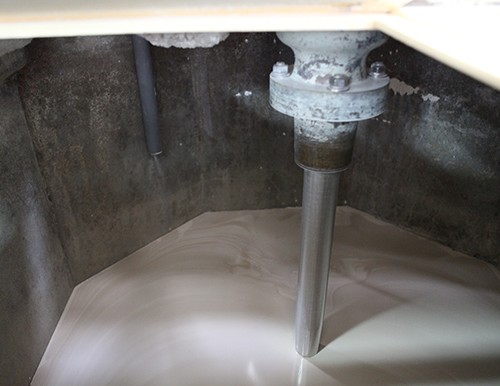
Les particularités de la porcelaine
La porcelaine se caractérise par un fort retrait (12 à 14%).
Le retrait est lié à deux paramètres :
– le départ de l’eau lors du séchage de la pâte, lors du changement de l’état physique des silicates du kaolin.
– la vitrification et à la cristallisation du kaolin sous forme de cristaux de mullite.
La pâte a tendance à se déformer et à s’affaisser à la cuisson. Elle possède aussi un effet «mémoire» qui l’amène à se déformer ou à se fendre à la cuisson si les manipulations de la pâte lors de la fabrication n’ont pas été suffisamment précautionneuses.
La pâte est vitrifiée et translucide, sa porosité est inférieure à 0,5%. La pâte est non friable et non gélive.
Des pâtes blanches, extra-blanches, ivoire et céladon on été développées au cours du temps. Aujourd’hui, la production est dominée par la pâte «extra-blanche».
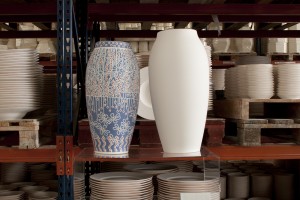
Les caractéristiques d’un objet en porcelaine ont été clairement définies par un décret, le seul encore en vigueur
Décret n°78-141 du 8 février 1978 portant application, en ce qui concerne le commerce de la porcelaine, de la loi du 1er août 1905 modifiée sur la répression des fraudes
«Il est interdit, sous réserve des dispositions de l’article 3, de dénommer « porcelaine », avec ou sans qualificatif, et de désigner par une dénomination contenant ce mot, ou des dérivés ou imitations de ce mot, des produits qui ne seraient pas constitués d’un mélange de matières kaoliniques, argileuses, fondantes (notamment feldspathiques), siliceuses et dégraissantes mis en forme avant cuisson par façonnage « en poudre », « en pâte » ou en « barbotine ».
Le corps de cuisson, émaillé ou non, doit être constitué de deux sortes de cristaux, mullite et quartz, et d’un verre feldspathique. La masse doit être soit blanche, soit colorée par adjonction de colorants minéraux.
Dans le cas de porcelaine émaillée une glaçure est superposée au corps de cuisson, et d’une nature distincte de celui-ci.
Le produit obtenu doit répondre aux caractéristiques suivantes :
Densité apparente supérieure à 2,20 ;
Porosité de la matière non émaillée ou désémaillée inférieure à 0,50 p. 100 ;
Translucidité sous une épaisseur comprise entre 3 et 4 mm.»
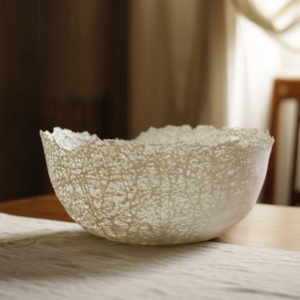
Les techniques de façonnage – le coulage
Aucune technique de façonnage purement manuel ne s’est véritablement développée à Limoges.
Aux prémices, une pâte plastique était appliquée par estampage sur des demi-coques en plâtre, puis ces empreintes étaient collées avec une barbotine.
Plus tard, l’utilisation de barbotine de coulage dans des moules démontables ont permis de diminuer le nombre de pièces défectueuses : coulage de revide ; moule entre deux plâtres. Ces techniques sont toujours employées de nos jours.
Il existe également des techniques de coulage sous pression : la pâte est envoyée sous pression dans des moules, ce qui accélère l’absorbtion de l’eau par le moule et permet ainsi de produire des pièces «entre deux plâtres» plus rapidement. La manipulation des pièces peut-être automatisée.
Les techniques de façonnage – le calibrage
Le calibrage de formes sur bosses s’est développé avec la machine Faure (1869), et plus tard, sont apparu les machines «roller» qui produisent les pièces en série pratiquement sans intervention humaine :
en creux (tasses, gobelets) en bosse (soucoupes, assiettes, etc.)
Les techniques de façonnage – le pressage
Le pressage se fait à sec, à partir de pâte atomisée (en poudre) ne contenant que 5% d’humidité.
Les moules sont en métal ou en matière de synthèse (polyuréthane).
Les techniques de façonnage – le garnissage et la finition
On réalise des pièces rapportées par coulage : anses, boutons, poignées…
Ces éléments sont collés sur pâte crue encore humide à l’aide de barbotine.
Lorsque la pâte est sèche mais encore crue, on procède à l’ébavurage des coutures à l’aide de fines lames et d’éponges humides, et au ponçage à l’aide abrasifs…
La cuisson – le dégourdi
La cuisson de dégourdi consiste en une pré-cuisson de la pâte à une température inférieure à celle de la cuisson définitive, entre 800 et 1000 °C.
Elle provoque l’évacuation complète de l’eau de constitution de l’argile, fixe définitivement une part du retrait de la pâte, la rend manipulable et facilite l’étape d’émaillage car la pâte reste poreuse.
La pâte prend alors une coloration rosée.
L’émaillage
La pièce dégourdie est prête à recevoir la couverte transparente caractéristique de la porcelaine avant la cuisson de grand feu. L’émail est une couverte vitreuse principalement composée de quartz et de feldspath, avec une petite proportion de kaolin.
On procède soit par trempage (manuel ou automatisé), soit par aspersion ou pulvérisation.
Enfin, la pièce est désémaillée aux zones de contact avec le matériel d’enfournement (plaques et gazettes réfractaires) afin de ne pas rester collée par l’émail devenu vitreux durant la cuisson.
Le décor – le grand feu
Bien que minoritaire, le décor de grand feu est pratiqué à Limoges.
La pose du décor de grand feu se fait sur une pièce dégourdie.
On applique un mélange d’oxydes métalliques sur les pièces dégourdies à l’aide d’un pinceau, ou en procédant par aspersion ou par trempage.
La couleur de grand feu la plus courante est le «Bleu de four» obtenu avec de l’oxyde de cobalt, mais d’autres couleurs sont possibles à partir d’autres oxydes métalliques.
La cuisson – le grand feu
Les pièces sont cuites à 1400°Celsius sous atmosphère réductrice.
Les assiettes sont placées dans des gazettes réfractaires de façon à pouvoir les empiler.
Les autres formes sont posées sur des plaques en céramique réfractaire.
Les fours sont à combustible pour les cuissons de haute température :
À l’origine, les fours utilisaient le bois, puis on employa le charbon (premiers essais en 1785 à Lille, utilisation industrielle à Limoges à partir de 1845).
Enfin, on employa le gaz (premiers essais en 1845, mais il ne fût définitivement adopté par les industriels qu’à la fin des années 1950). Ce combustible est toujours en usage aujourd’hui.
L’utilisation d’un four à combustible est indispensable pour le grand feu car lui seul permet de maîtriser l’atmosphère de cuisson. Le four électrique, puisqu’il ne consomme pas l’oxygène, ne cuira jamais parfaitement la porcelaine. C’est pour cette raison que les industriels emploient toujours des fours à gaz pour la cuisson de grand feu.
Photo Un four à flamme renversée, alimenté au charbon, source : Le feu, les fours, la porcelaine, de Jacques Coudamy, 1987.
Photo Un four à gaz de petite dimension : environ 1m3, Porcelaines Chastagner, photo. Matthieu Bussereau.
Photo Un four à gaz de grand volume : environ 12 m3, photo. Porcelaines de la Fabrique.
Finitions et contrôle qualité
Les formes reçoivent une ultime finition : le pied des pièces est poli.
Les pièces sont alors scrupuleusement contrôlées : déformation, fente, défauts d’émaillage les écartent de la production.
Les pièce sont classées selon leur qualité. Les pièces de la meilleure qualité constituent le «premier choix», les pièces de qualité intermédiaire constituent le «second choix» ou le «déclassé», et enfin, les plus mauvaises sont détruites.
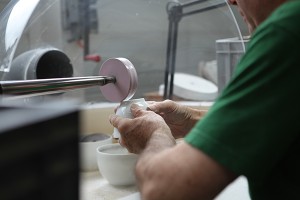
Le décor – le petit feu
La fabrication de la forme («le blanc») est séparée de celle du décor :
Les formations, les métiers, les corporations, les ateliers et même parfois les entreprises ne sont pas les mêmes. Cette séparation existe depuis l’origine et se ressent toujours aujourd’hui.
La technique originelle est celle du décor posé à la main :
– fonds de couleur putoisé ou uni,
– motifs et figures réalisés au pinceau, à main levée ou à l’aide de poncifs,
– filets de couleur ou de métaux précieux réalisés au pinceau.
Ensuite sont apparues des techniques permettant de produire des décors en série : la chromolithographie. C’est un procédé d’imprimerie qui fonctionne comme une décalcomanie faite à partir de couleurs céramique. Les plus grandes manufactures peuvent avoir leur imprimerie intégrée.
Le décor – l’incrustation et le brunissage
La décoration par incrustation consiste à graver un décor directement dans l’émail en utilisant de l’acide fluorhydrique, après avoir préalablement protégé les parties en réserve grâce à du bitume de Judée.
Le plus souvent, ce décor en relief est rehaussé avec des métaux précieux : or ou platine.
L’or et le platine sont polis à la pierre d’agate et au sable de Nemours afin d’obtenir une meilleure brillance. Cette étape s’appelle le brunissage.
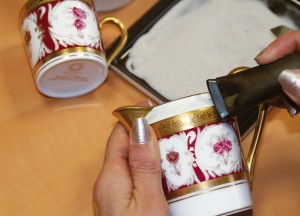
La cuisson – le petit feu
A l’origine, la cuisson du décor se faisait dans des petits fours à bois ou à charbon, jusqu’à la deuxième guerre mondiale environ.
L’apparition du four électrique s’est fait quand la métallurgie a pu développer des résistances électriques en alliages de chrome et de nickel suffisamment résistants à la chaleur. Ce ne sont plus des fours à combustible, mais des fours à rayonnement.
Les premiers essais ont eu lieu dans les années 1940, et le développement de ces fours s’est fait dès les années 1950, en même temps que l’augmentation du nombre d’ateliers de décor. Ils sont très utilisés aujourd’hui.
Les fours électriques ont constitué un progrès pour les cuissons de décor, permettant deux cuissons par jour en four intermittent ou la cuisson en continu avec l’apparition des fours tunnels, mais ils demeurent inadaptés à la cuisson de grand feu du «blanc».
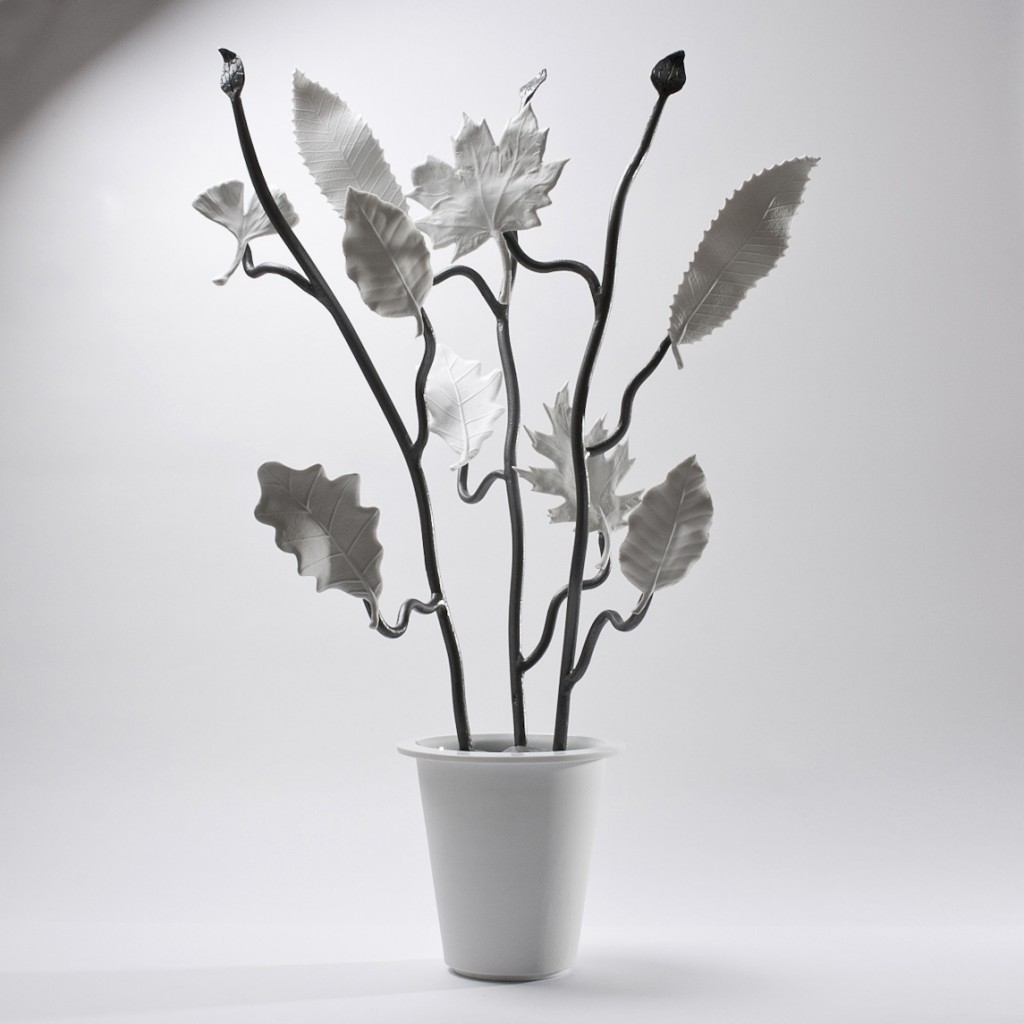
History and production of Limoges porcelain
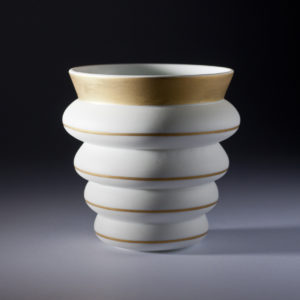
Birth of the appeal of the porcelain material
Since the beginning of the Christian era until the seventeenth century, exotic Chinese objects sought, rare and expensive, are transported to Europe by land (Silk Road) or by sea opened by Marco Polo.
While the fascination with porcelain grows throughout Europe, a Jesuit, Father François Xavier d’Entrecolles, born in Limoges February 25, 1665 and died in Beijing July 2, 1742, reported by a detailed account manufacturing porcelain in China, in 1712 and in 1722. This story describes many stages of pulp manufacture, shapes, decor, ovens … but it does not completely penetrate the secret of porcelain.
Across Europe develops the will to produce porcelain « will rival that of the East Indies »
This is in Meissen, Saxony (now Germany) as Johann Friedrich Böttger, an alchemist, pierces the secret of porcelain in 1710.
In 1751, the factory Paul haunt a hard porcelain factory in Strasbourg.
Mark of the ore and the development of the dough
We now know that kaolin deposits form at the expense of the primary decomposition of granitic rocks (rocks acids) found in several regions of France: Limousin, Auvergne, Brittany, Drôme …
Discovered in 1768 in the towns of Saint-Yrieix-la-Perche, then those of Marcognac, Saint-Paul-la-Roche, La Jonchère-Saint-Maurice … the presence of kaolin finally opens the way to the kingdom of France to manufacture its clean porcelain.
Tests are conducted in Sèvres and Limoges. Sèvres produces hard porcelain in 1765 and Limoges manages to produce a hard porcelain in 1771.
The first Limoges porcelain factory is actually a « Fayancerie Royalle » based in Limoges in 1736 by Massie. It is at this working earthenware with a royal amusement we began manufacturing and baking tests of Limoges porcelain from 1770.
The development of porcelain factories became from 1773:
Fabrique du Comte d’Artois (1773), The Seynie (1774), Manufacture Royale (1784), Monnerie (1795) Alluaud (1797), Tharaud (1817), The Fabric of St. Brice (1825), Coussac-Bonneval (1825), Pouyat (1832), etc.
Factories are born and die, be bought, sold, modernize, move … but some of them are still in business today.
The first factories and their strong development during the nineteenth century
The growth of manufacturing has been selling porcelain throughout France, especially the complete dinner services for weddings; and also export abroad, especially to the United States.
Year | 1837 | 1875 | 1913 |
---|---|---|---|
Manufactures | 24 | 20 | 30 |
Hovens | 40 | 85 | 114 |
Workers | 4550 | 8450 | 8200 |
Turnover | x | 4 750 000 | 11 800 000 |
The example of Haviland
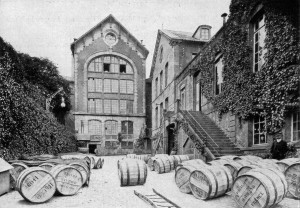
Year | Number delivered packages |
---|---|
1842 | 753 |
1843 | 909 |
1844 | 1847 |
1845 | 1630 |
1846 | 2087 |
1847 | 2650 |
First buyer of white, Charles Haviland secured the scene before sending the bulk of its production to the USA, where his sets were designed and where he enjoyed an excellent distribution network. To cope with its tremendous success, he formed many decorators and began to produce his own white porcelain.
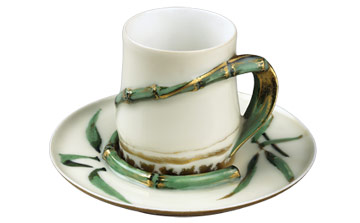
In the nineteenth century built an industrial fabric conducive to the activity of manufacturing
Several kaolin mines are opened in Haute-Vienne, and kaolin dryers and mills which processes the raw materials and preparation of pasta.
There were 16 mills in operation in 1837.
« The Factory of the castle » in Aixe-sur-Vienne, very old mill pulp, is still operating under the name KPCL (Kaolin and Pasta Limousin Ceramics), Imerys group.
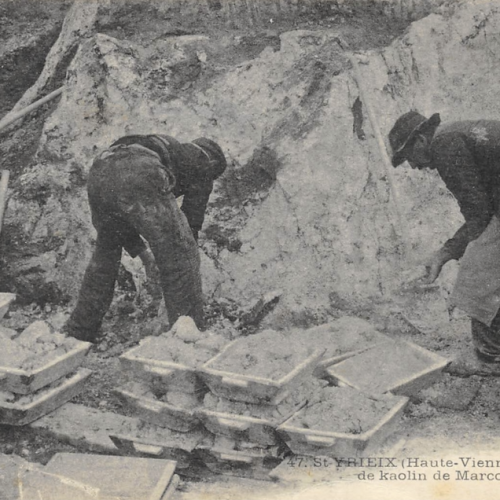
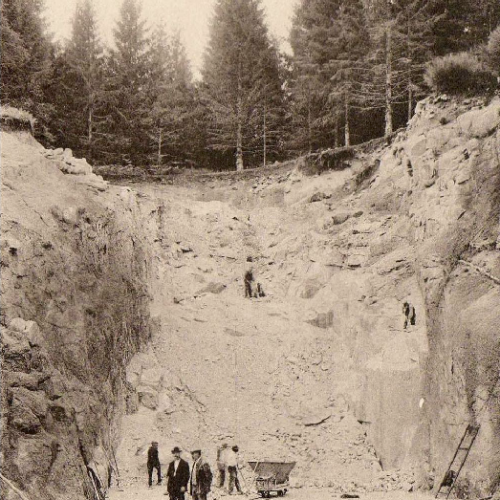
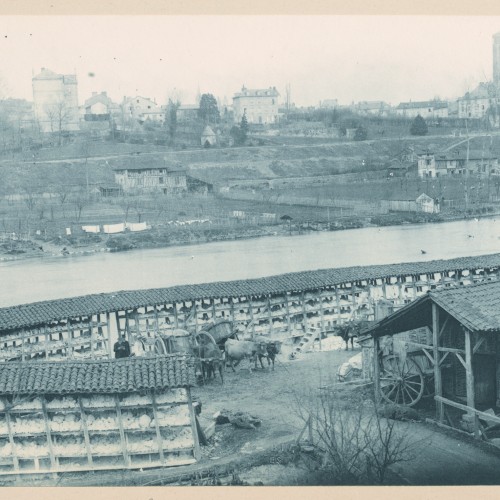
The wood needed for cooking
Wood was cut by loggers in Creuse (neighboring department) or in the east of Haute-Vienne, several tens of kilometers, before passing over several river tributaries to reach Vienna Limoges where wood was stopped by a dove. Loggers and wood floats were a powerful corporation because their activity was decisive for the porcelain industry.
Year | Floated wood volume over the Vienne |
---|---|
1789 | 10 000 stères |
1814 | 23 000 stères |
1855 | 107 000 stères |
1865 | 45 000 stères |
In 1881, timber floating stopped in favor of transportation ferroviaire.En 1897, the dove of Limoges was demolished.
Industrial activity in the nineteenth and twentieth centuries
The porcelain industry has experienced delays in its development during the 1870 war, and during the two World Wars.
Production declined in 1914-1918 for the sake of the war effort and lack of manpower, the men away at the front.
In 1939-1945, production was even more sharply for reasons of restrictions related to the war effort and to occupation: more than enough raw materials, restrictions on coal and wood …
But after each difficult period, Limoges manufacturers have quickly returned to growth and profits.
Industrial activity after 1950
1950 to the present, the factories employ designers Raymond Loewy, Roger Tallon, Marc Held, Martin Szekely, Olivier Gagnère, Hervé Van Der Straeten, Andrée Putman, Jean-Charles de Castelbajac, Sylvain Dubuisson, Andrea Branzi, etc. .
From 1980, consumption habits have changed and the industry experienced a sharp decline in sales. Many companies had to be restructured or disappeared.
Today, manufacturers are condemned to reinvent itself by diversifying their activities on luxury, jewelry, decorative objects, partnerships with designers, while still producing the traditional table service.
The main market players today
- About 20 companies at present
- 1100 direct jobs in Limoges porcelain companies
- 300 induced jobs
- About 120 million euros of annual turnover
- 70% of production export share, the majority of the US
- The most famous manufactures are: Bernardaud, Haviland, Raynaud, Royal Limoges, R. Haviland & C. Parlon, J. Seignolles, Arquié, Carpenet, Pergay, Medard de Noblat, Jean Louis Coquet Sylvie Coquet …
The action Esprit Porcelaine for 30 years, bringing together established artists and younger generation.
Creators mind Porcelain Limoges is a collective of designers ceramists who imagines the objects of today and tomorrow. By mixing different artistic backgrounds: designers, craftsmen, designers forms, artists … the association has a creative dynamic in perpetual renewal.
Artists Vivier, laboratory of ideas, the creators of Ghost Porcelain -through personal features that are always going in the direction of innovation -oeuvrent in a constant concern for the image they want to develop renewal Limoges porcelain.
Anchored in its territory Spirit Porcelain cooperating closely with local companies for the production and editing of its models.

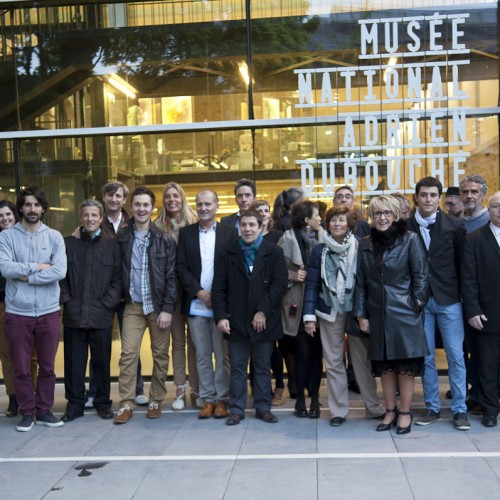
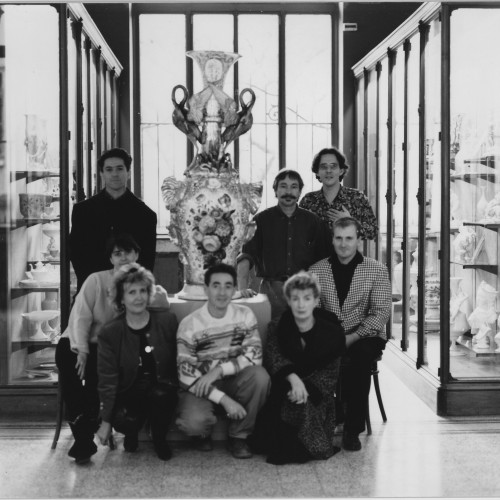
The formation of ceramic and porcelain in Limoges tomorrow
High School of Arts and Crafts « The Jambost Mas »
– Occupation Patent artisanal ceramics Art
– Certificate of Professional Competence of decoration on ceramic
Association of Vocational Training for Industry
– Higher National Diploma in industrial ceramics
National School of Art
– Higher national diplomas in art and design
– Post-degree in contemporary ceramics
National School of Industrial Ceramics
– Industrial Ceramic Engineers
A PGI (Protected Geographical Indication) to Limoges porcelain
A project PGI (Protected Geographical Indication) aims to establish labeling and check the provenance of products stamped « Limoges Porcelain -France » to prevent counterfeiting and fraud, and protect local industry. This label requires that the product is completely manufactured in the department of Haute-Vienne: manufacture of form and decoration.
Manufacturing – Plaster
Gypsum is the main material for the creation of forms. It is used for both models for molds, plaster metering options giving it great versatility.
For the realization of models, we can cut, carve and sculpt the plaster, but also drag and rotate it using templates, templates and tournasins.
Plaster, its porosity, is ideally suited to the production of molds for porcelain: the plaster mold gives shape while it absorbs moisture; it can be used to make prints on sculpted models, or from « nature ».
In principle, and because of the decisive nature of the workshops, each factory has its mold shop where one works plaster. This is a separate workshop from the other to prevent the plaster from contaminating the porcelain paste. This is also the workshop, which expresses the creative nature of each factory.
In this workshop working modellers, who create forms templates and sample molds.
Since the molds can only be used 30 to 50 times, it must be renewed regularly. It is for this reason that the dies are made to duplicate and renew the molds.
After the modeler takes the établisseur. He made the first mold and dies from models or samples molds. The dies are made of plaster, resin or silicone.
The mold of color produces the molds in series from the matrices.
The work of modelers and établisseurs is essential in any factory, and as this know-how is specific, it can be carried out only by specialist staff.
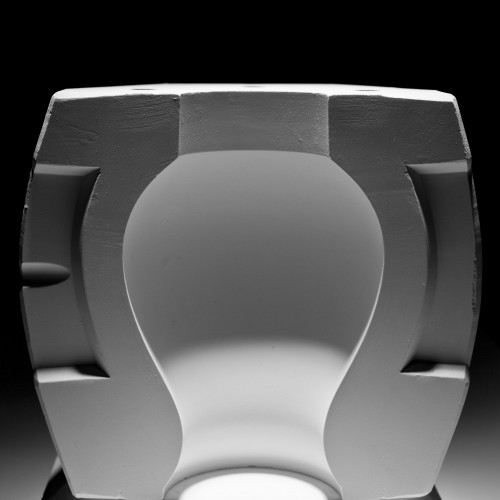
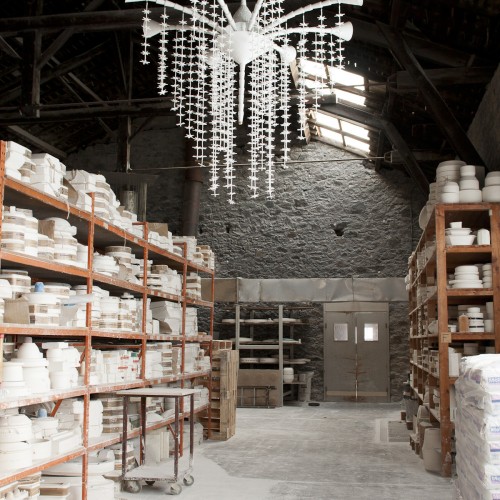
Manufacturing – Dough
The porcelain is not a « land » existing in nature, but a « dough » human-engineered from three main rocks:
kaolin, quartz and orthoclase pegmatite.
The overall composition is:
50% of kaolin
25% of feldspar
25% quartz
In the slurries, a small amount of deflocculant is added (sodium carbonate, sodium silicate) which allows the paste to be the fluid with the minimum of water, and which prevents it from freezing.
Kaolin is a primary refractory clay. It turns into mullite crystals immersed in a vitreous mass of fused quartz at the high temperature firing.
It accounts for 50% in the composition of the dough.
Orthoclase pegmatite is a potassium rock having the effect of lowering the vitrification point of the dough.
It contains feldspar and quartz and between 40% in the composition of the dough.
Quartz between 10% in the composition of the dough.
Very refractory, it becomes glassy around 1380 ° C, with the feldspar used fondant.
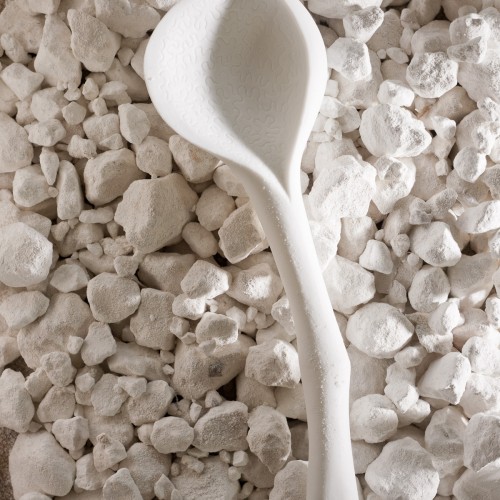
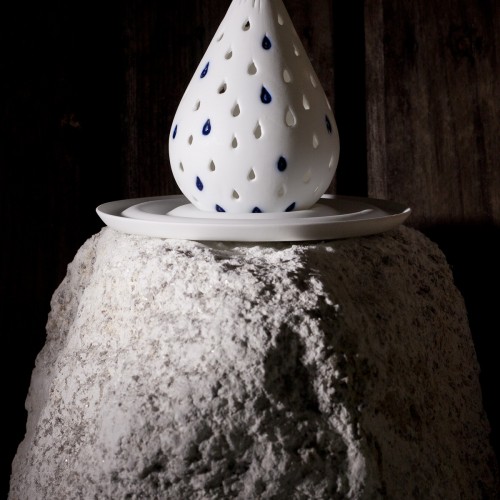
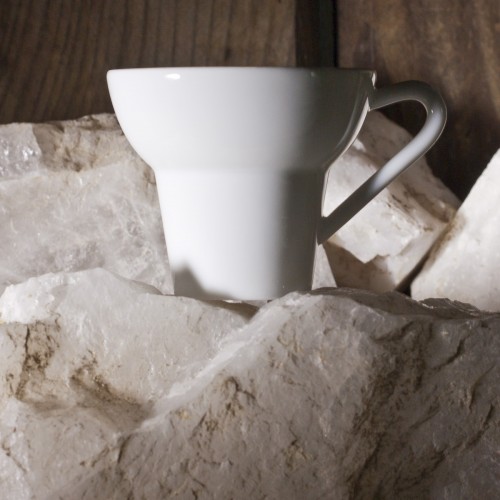
The various forms of the dough
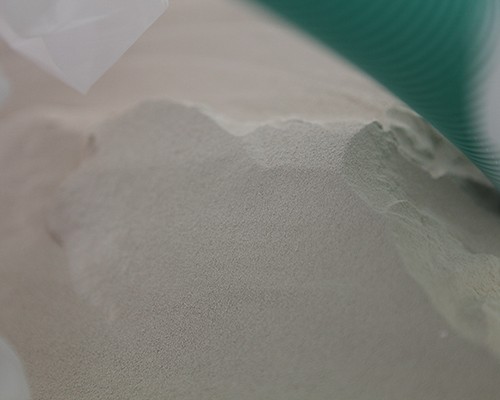
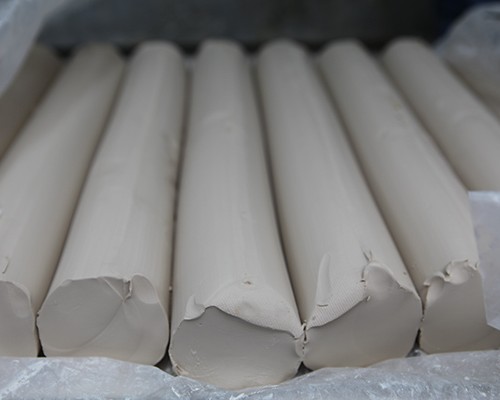
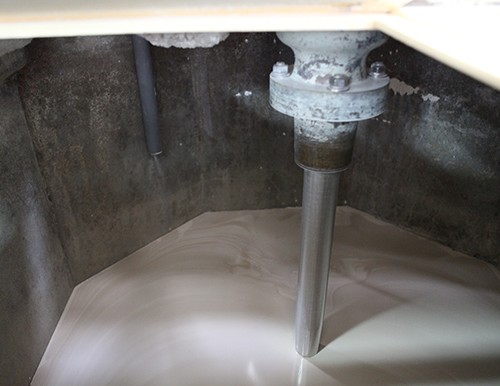
The porcelain particularities
The porcelain is characterized by a high shrinkage (12 to 14%).
The shrinkage is related to two parameters:
– The departure of the water during the drying of the dough, when changing the physical state of kaolin silicates.
– Vitrification and crystallization of the kaolin in the form of mullite crystals.
The dough tends to distort and sag while cooking. It also has a « memory » effect that causes it to deform or crack during cooking if the manipulation of the dough during production were not enough Cautiously.
The paste is vitrified and translucent, its porosity is less than 0.5%. The dough is not crumbly and not freeze.
White pasta, extra-white, ivory and celadon have been developed over time. Today, production is dominated by the « extra-white » paste.
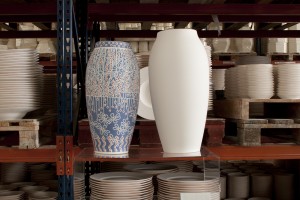
The characteristics of a porcelain object has been clearly defined by a decree, the only one still in force
Decree No. 78-141 of 8 February 1978 implementing, as regards trade in porcelain, the law of 1 August 1905 amended Fraud
« It is forbidden, subject to the provisions of Article 3 of styling » china « , with or without qualification, and designate by a name containing the word, or derivatives or imitations of the word, of products which are not not made of a mixture of kaolinitic materials, clay, soft (including feldspar), siliceous and degreasing shaped by shaping before curing « powder », « paste » or « slip ». The cooking body, enamelled or otherwise, must be composed of two kinds of crystals, mullite and quartz, and feldspathic glass. The mass shall be either white or colored by adding mineral dyes.
In the case of a porcelain enamel glaze is superimposed on the cooking body, and a distinct nature thereof.
The product must meet the following characteristics:
bulk density higher than 2.20;
Porosity of unglazed material désémaillée or less than 0.50 percent. 100;
Translucency in a thickness between 3 and 4 mm. «
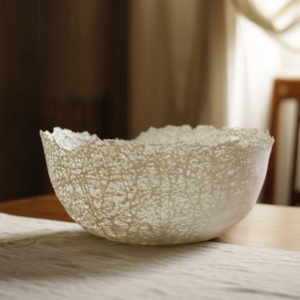
Shaping techniques – casting
No shaping technique purely manual only really developed in Limoges.
The beginnings, a plastic paste was applied by stamping on plaster half-shells, then these prints were glued with slip.
Later, the use of slip casting in demountable molds have reduced the number of defective parts: revised last casting; mold between two casts. These techniques are still used today.
There are also die-casting techniques: the pulp is sent under pressure into molds, which accelerates the absorption of water by the mold and allows to produce parts « between two casts » faster. Handling parts can be automated.
Shaping techniques – calibration
The calibration forms Mogul has developed with the Faure machine (1869), and later appeared the « roller » machines that produce the parts in series almost without human intervention:
Hollow (cups, tumblers) bump (saucers, plates, etc.)
Shaping techniques – pressing
Pressing is dry from atomized paste (powder) containing only 5% moisture.
The molds are made of metal or synthetic material (polyurethane).
Shaping techniques – the packing and finishing
Is produced by casting patches: handles, knobs, handles …
These elements are glued on wet uncooked dough using slip.
When the dough is dry but still raw, there follows the trimming seams using thin blades and wet sponges, and abrasive sanding to help …
Cooking – le dégourdi
Dégourdi cooking consists of a pre-baking of the dough at a temperature lower than the final cooking, between 800 and 1000 ° C.
It causes the complete evacuation of clay incorporation of water, a permanently fixed part of the paste is removed, makes the handle and facilitates the enameling step because the dough remains porous. The dough takes on a pink color.
Enameling
The unglazed piece is ready to receive the transparent characteristic of the porcelain before firing bonfire covered. Enamel is a vitreous glaze mainly composed of quartz and feldspar, with a small proportion of kaolin.
Be obtained by either soaking (manual or automated) or by sprinkling or spraying.
Finally, the piece is désémaillée the areas of contact with the kiln furniture (refractory plates and newspapers) to not stay stuck with vitreous enamel became during cooking.
The decor – the great fire
Although minority, the decor of large fire is practiced in Limoges.
The installation of high-fired decoration is on a unglazed piece.
Applying a mixture of metal oxides on the dégourdies parts using a brush, or by carrying out by spraying or by dipping.
Color large fire most common is the « Oven Blue » obtained with cobalt oxide, but other colors are possible from other metal oxides.
Cooking – the great fire
The pieces are fired at 1400 ° C in a reducing atmosphere.
The plates are placed in refractory newspapers so as to stacking.
Other forms are placed on plates of refractory ceramic.
The ovens are fuel for high temperature cooking:
Originally, the ovens used wood, then coal employed (first tests in 1785 in Lille, industrial use in Limoges from 1845).
Finally, we used the gas (first tests in 1845, but it was finally adopted by the industry in the late 1950s). This fuel is still in use today.
Using a fuel furnace is indispensable for the great fire for he alone will control the firing atmosphere. The oven, since it does not consume oxygen, never cook perfectly porcelain. This is why manufacturers still use gas ovens for baking large fire.
Finishes and quality control
Forms receive the ultimate finish: the foot parts is polished.
The pieces are then carefully controlled: deformation, crack, enamel defects apart from production.
The room are classified according to their quality. best quality parts are the « first choice », the intermediate quality parts are the « second best » or « decommissioned », and finally, the worst are destroyed.
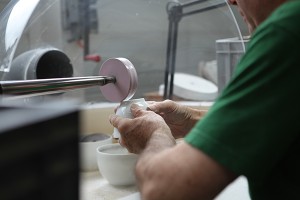
The decor – the small fire
The manufacture of the form ( « white ») is separate from the decor:
Trainings, business, corporations, workshops and even businesses are not the same. This separation has been the origin and is still being felt today.
The original technique is the decor laid by hand:
– Colored backgrounds putoisé or united,
– Patterns and figures made by brush, freehand or using clichés,
– Color nets or precious metals carried by brush.
Then appeared techniques to produce series decorations: chromolithography. This is a printing process that works like a decal made from ceramic colors. The largest factories may have their integrated print.
The decor – keying and burnishing
The decoration with inlay is to burn a decor directly in the enamel using hydrofluoric acid, after previously protected parts in reserve with bitumen of Judea.
Most often, this relief decoration is accented with precious metals: gold and platinum.
Gold and platinum are polished with an agate stone and sand from Nemours to get a better gloss. This is called burnishing.
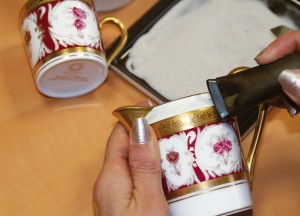
Cooking – the small fire
Originally, cooking decor was done in small ovens to wood or coal until the second world war about.
The appearance of the electric furnace is made when the metal was able to develop electrical resistance alloys of chromium and nickel sufficiently resistant to heat. No longer fuel ovens and radiation ovens.
The first tests took place in the 1940s, and the development of these furnaces was done in the 1950s, along with the increasing number of decor workshops. They are widely used today.
Electric furnaces have made progress for decoration firings, allowing two firings per day in intermittent furnace or continuous cooking with the appearance of tunnel kilns, but they are unsuitable for cooking large fire « white. »
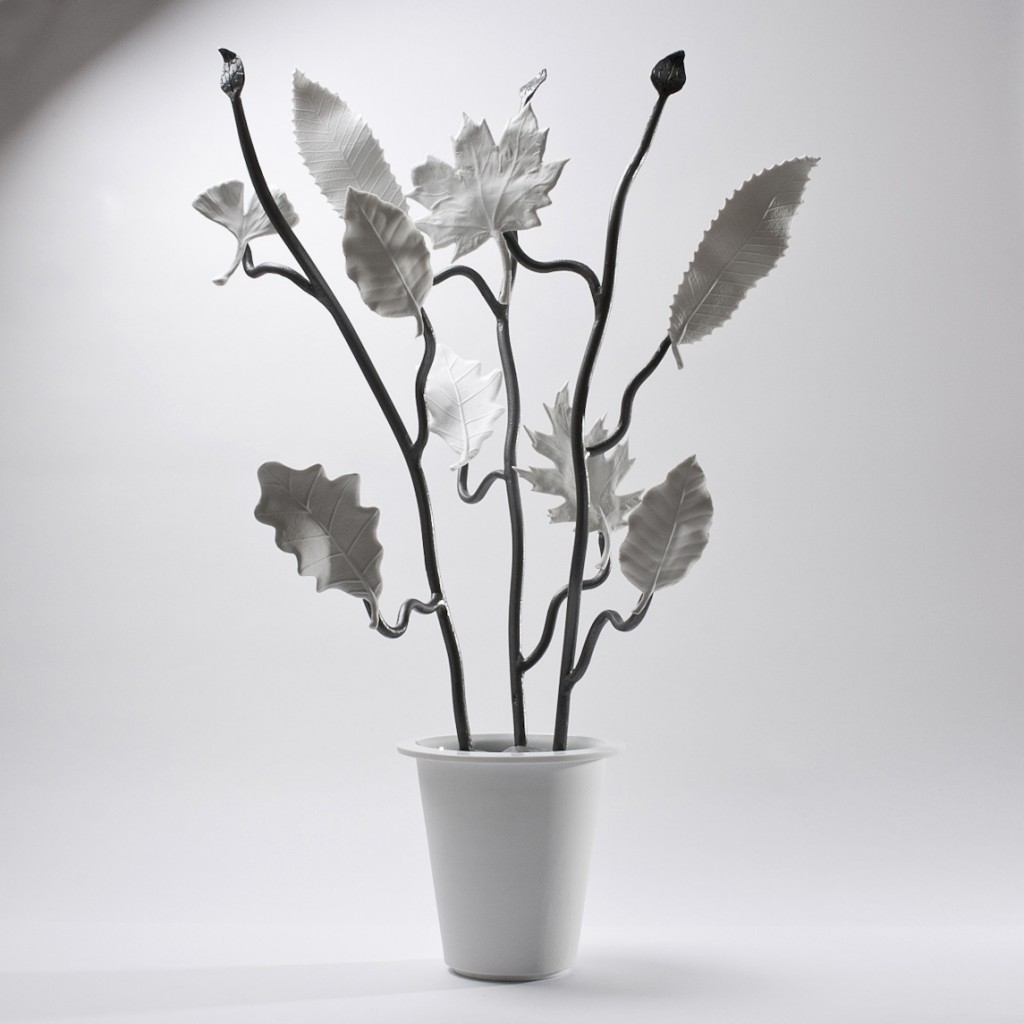